We’ll be taking a detour today from our CNC benchtop mill project for a quick “one afternoon” build for the Kearney & Trecker 2HL vertical mill. The Milwaukee was missing its y-axis hand wheel when I purchased it, but I figured at the time that I could pick one up cheap off of Ebay. After a couple of months of searching, I discovered that this was not the case and decided to machine one myself from a blank.
The design of the K&T hand wheel and crank is relatively simple. A boss extends (on my machine) 3/4 of an inch from the back of the wheel and passes through the throw levers for the table feed. It engages what I suppose is the y-axis screw by way of four teeth cut in an “X” configuration.
The shaft of the screw passes through the wheel, which allows it to slide on and off to engage the teeth when desired. The boss is just the right size to keep the feed lever from engaging while the hand wheel is engaged and vise-versa: while the lever is engaged, the hand wheel teeth can’t engage the screw.
After a bit of searching, I found a surplus blank that seemed to be a good candidate. Although it was missing the spinning handle, it had enough meat on it to turn the required 3/4″ (L) x 1-3/16″ (W) boss on the back side. Many of the blanks I saw online did not have enough material to do this, so my advice to anyone replicating this relatively simple project would be to make sure you can get a measurement of the wheel back side before purchasing a blank.
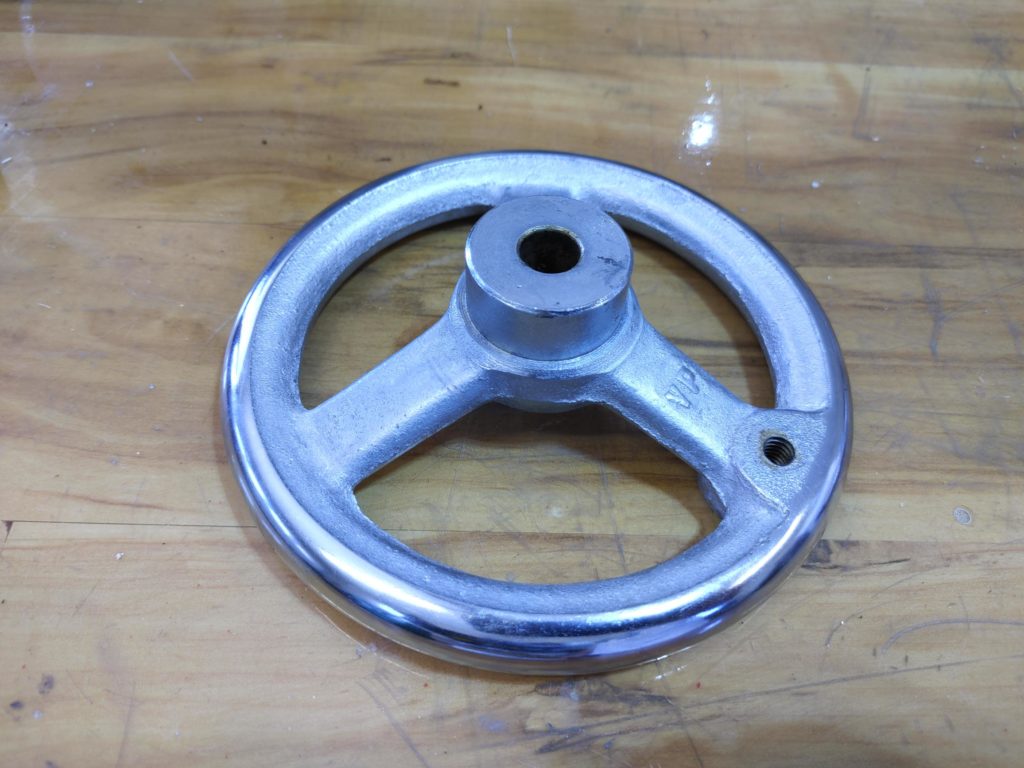
The first step was to secure the wheel in my LeBlond three-jaw chuck (with reversed jaws) and turn down the boss. I used a bit of tape to keep the jaws from marring the chrome.
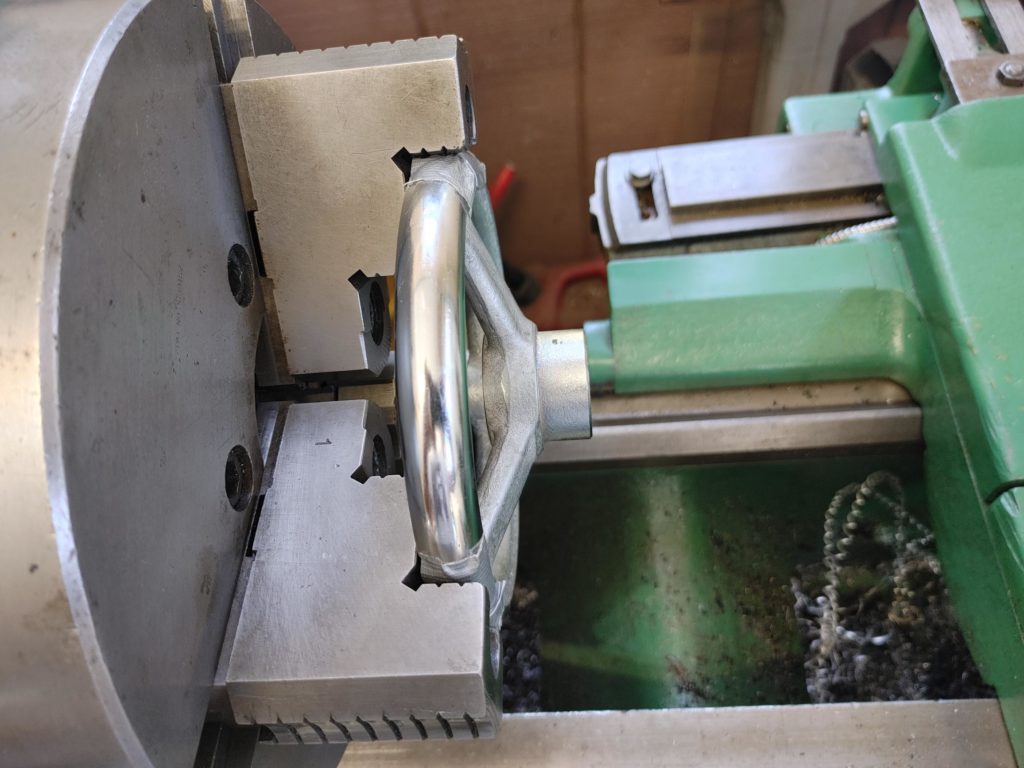
Here it is turned down to the 3/4″ x 1-3/16″ dimension.
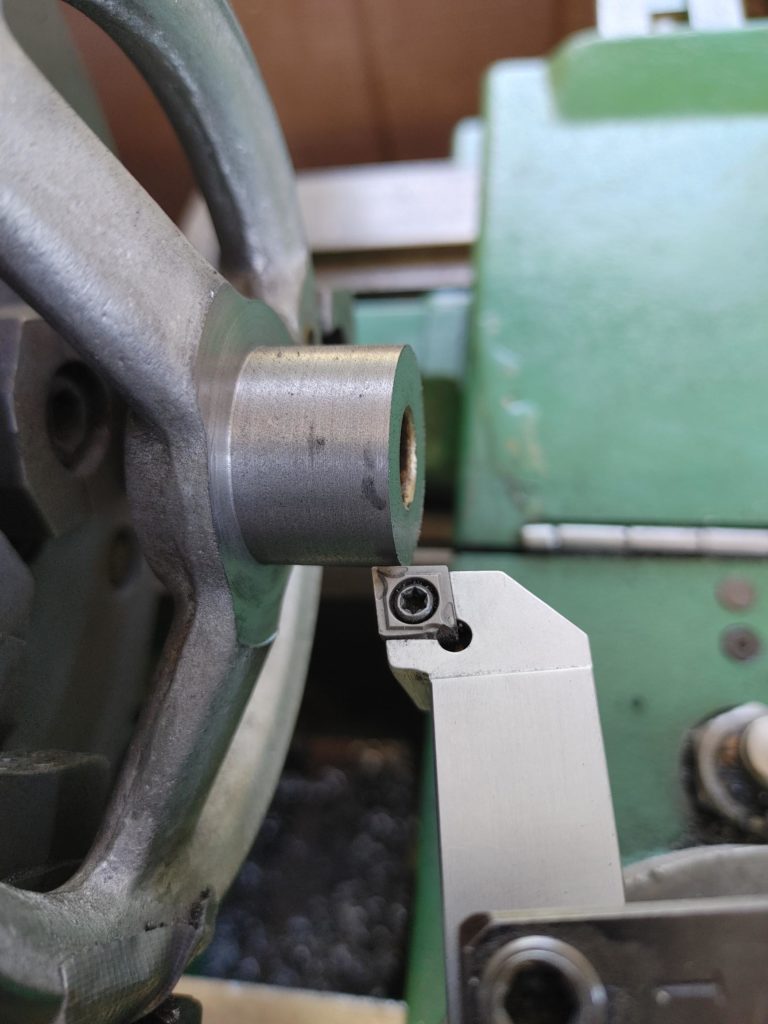
Next, I expanded the 1/2″ bore to 5/8″, which provided enough clearance to slide up and down the end of the screw shaft.
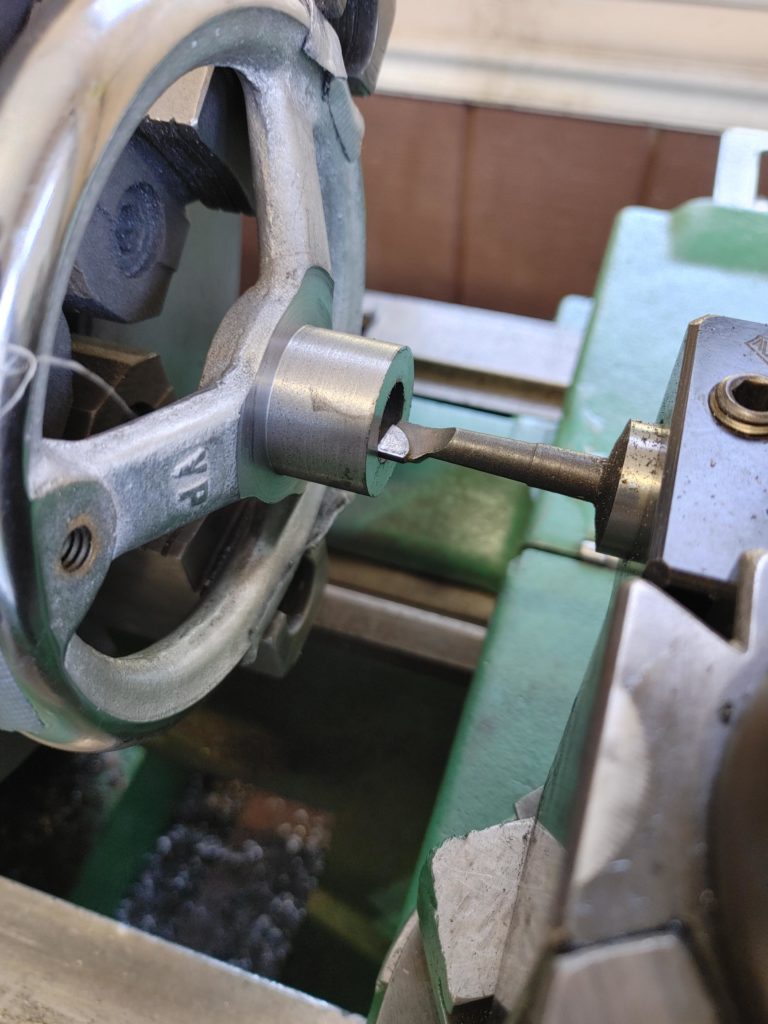
With the boss turned to the correct length and width, and the shaft hole bored, the next step was to cut the four teeth that engage the end of the screw in an “X” pattern. This can be done by finding the center of the bore, then making two quick passes of a 5/16″ mill: one along the x-axis and one along the y-axis.
I cut the tooth depth to about .2″. If I had it to do over, I’d reduce that to 3/16″ — at the depth I cut them, it allows the wheel to rub slightly on the table feed lever if I’m leaning into it.
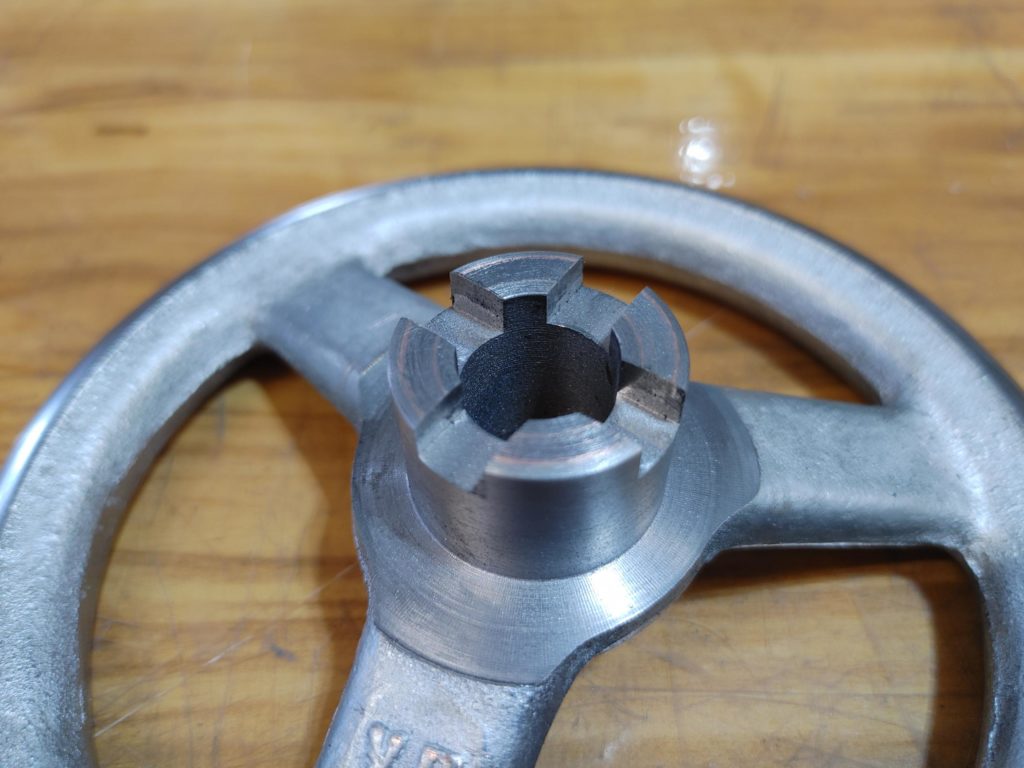
No biggie, though. As a final step, I found a 5/16″-18 thread handle cheap off of Ebay, which completed the assembly. All-in, about a $45 project. It engages great, and, well, turns like a wheel is supposed to.